Envirotech project
After speaking with James in person more in depth I brainstormed these possible ideas...
-
They are willing to try Google Drive again for inventory
-
Lock parts room after parts are gathered
-
Put barcodes on parts
-
Make a new app, willing to pay monthly if it means that the time and money for gas will be decreased
-
Figure out a way for an alert to go on the computer not only when they sell a part (like they have now), but also when a part is taken from the shop
-
Have a par level inventory system
-
Check if there is a way to see a summary and restock exactly then verify in the office
-
Look at the “My Inventory section of the Aptora total office manager software they’re currently using
-
Request an Aptora demo and look at their youtube for further help
-
research different ways that successful companies have kept their field workers accountable to restocking their trucks/how they have reminded them without giving an extra job to someone else
Internship
At my internship, I helped ideate quite often. If I wasn't helping, I always paid attention to the ideas other high up people had...
-
I helped figure out how we could package things and make the labels for certain trucking companies that would deliver the parts to their customers.
-
I ideated different ways for assembly lines to be made on the CAD modeling and how existing machines can be moved around to fit our systems.
-
I thought of ways that I could get a good educational experience at Baader while staying out of their way when they are busy and being in certain departments when they needed help the most.
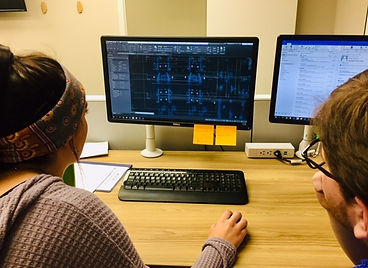
This is me helping Nick figure out how to fit an assembly line in a Tyson Chicken Plant and where exactly things should go to make it efficient.